I was born and spent half of my life in urban Odisha and have always been proud of my motherland. With it's unique language, literature, music, dance, and food, the state is culturally rich. Modern civilization has not fully killed the appetite for age-old traditions. Remote parts of Odisha mostly belong to tribal communities, who have kept their simple living habits alive, and kept their needs limited to what mother nature offers in the surrounding environment. They worship nature through every aspect of life. One such aspect they have kept alive is weaving. Widely known for their ikkat and other handloom weaves, different regions of Odisha have preserved the centuries-old weaving methods and are known for their use of cotton, silk, and tussar for various garments.
I always find that extra oomph with handwoven fabrics. I have yet to figure out what it is that makes me so emotional and nostalgic about it. Maybe I had never seen my mother wearing anything other than handloom sarees. So I find her warmth in every handwoven piece. I find them very classy and they feel good on my skin. And in my heart, I have satisfaction in knowing that flaunting them is helping someone somewhere to keep alive the traditional art form.
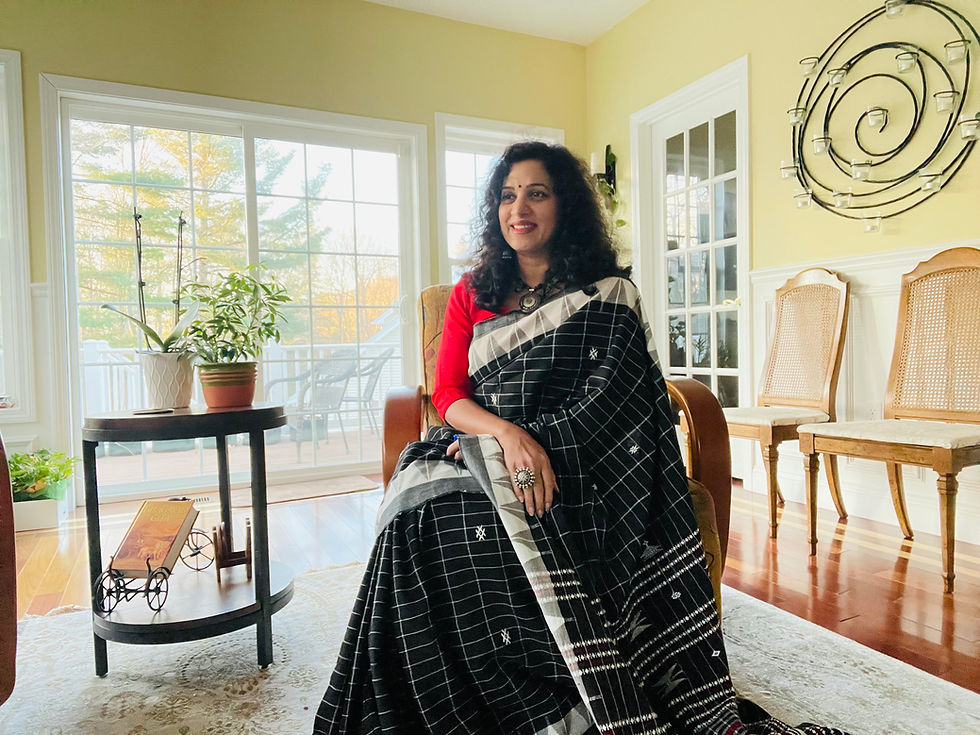
Here I am wearing Kotpad cotton sarees. Oh! How can I express in a few words what a kotpad saree is? It is just not 6 yards of fabric. Rough and coarse to touch yet soft on the skin, the kotpad weave is a story that speaks for itself. Though simplicity is the word

to describe its look, the process of making it is highly complex. Kotpad is one of the last remaining textile traditions of India which uses organic, eco-friendly, and non-toxic natural dyes. So it stands unique on its own merit.
Kotpad sarees are the pride of Odisha’s rich tribal weaving culture from the Koraput district of Odisha. It is one of the few things from Odisha that got a GI tag in the year 2005. The Kotpad weave was not discovered until the 1980s; it was showcased during the Festival of India’s Viswakarma exhibition. Since then it has slowly and surely gained popularity.
It is mainly the ‘Panika’ tribe who started weaving their own clothes. The Kotpad weavers are also called ‘Mirgans’. Originally there were eight small villages that inherited this skill of weaving from their forefathers though there is no historical documentation regarding its real antiquity. However, later another thirty villages in Nabarangpur area started adopting the style by acquiring that weaving skill. But it was not enough to keep up with the demand due to the tedious and time-consuming process of making these sarees.
Material:
Cotton yarn, Tussar silk, and Aul tree roots and barks, and other eco-friendly, non-toxic natural resources are the defining ingredients used for this textile. The coarse yarn is treated with cow dung, wood ash, fermented rice water, and castor oil in elaborate and laborious dyeing and drying process which takes up to a month. Despite the use of castor oil, there is no shine or smell. The yarn is dyed with the reddish tinge of the roots of the Indian Madder ('Aul' or Morinda citrifolia) tree. The color palette ranges from deep maroon to dark brown which is obtained depending upon the degree of aging of the 'Aul' and the way the dye is processed such as under the sun or in clay pots etc. Sometimes they also add Heerkashi and Harada to obtain the desired color. It takes approximately 15 to 30 days for processing the color and dyeing threads into different colors. Dyeing materials are prepared only during the dry months that makes their looms idle for almost four months.
Process:
The weaving process and the components are distinctly different from other Indian weaves. It is done in a simple but highly evolved three-shuttle pit loom with extra weft patterning for the more complicated motifs. The pit loom is a horizontal ground-staked handloom at which the weaver sits in a pit dug below floor level. Most lengths & specifications are measured perfectly by the portions of the Kotpad weaver’s fingers, the length of the palm & other sections of the arm, from fingertips to shoulder. The weaving involves both hands and feet and is rigorous and time-consuming. It takes about three months to weave a Kotpad saree. The weave can be identified by its trademark simple patterns like fish, leaf, hut, boat, axes, etc which reflect the cross-cultural linkage of the area and a distinctly different temple border.
The yarn used is of fairly thick count. It makes sense as the hilly region is fairly cold and this tight weave fabric is sure to keep them warm and for summer months more absorbent for perspiration. The local tribes use their weave in their daily life in the form of sarees, dhotis, towels, and shawls. The design and motif on these vary depending on the purpose of the textile - from a simple saree worn every day to one with rich motifs for weddings. The Kotpad sarees and shawls are examples of their brilliant craftsmanship.
Gaining popularity:
One of the master weavers, Kapileswar Mohonto, received national awards from the then-president Abdul Kalam Ajad for 2002-2003-2004, gaining attraction. Biswanath Rath, an Indian film director and producer, made a documentary on the weaver's fight for survival, ‘Kotpad Weaving: The Story of a Race Against Time’, which captured in depth the essence and beauty of this textile, along with the process. The documentary was telecasted on DD National in 2018. The documentary earned many accolades which attracted different fashion designers to take interest in this textile and Kotpad made it to fashion ramps. This documentary is a must-see for everyone who cares about preserving our age-old traditions. Lately, Gobardhan Panika, another master weaver of the craft, was honored with Padma Shri, the fourth highest civilian honor, by the Government of India in 2018.
By now kotpad sarees are known globally for sure but enough needs to be done to preserve the indigenous craft. A time-bound tedious process and scarcity of raw materials make this saree an expensive affair. The availability of synthetic fabrics as a cheaper alternative through modernization and an alarming decline in kotpad weavers and dyers present challenges in preserving this dying art and consequently paralyzing the local economy. Due to the painstaking method, mass production is not an easy option unless more weavers are trained in the craft. Despite all this, this ageless art of handloom weaving has stood the test of time for centuries.
In close, be a consumer or be a sponsor, adopt a village or preserve the plantation for required trees, or just try your best to be a positive influencer. Recently I saw Bibhu Mahapatra, the doyen of fashion designers based in New York, design outfits for an opera using Kotpad fabrics. Lipsa Hembram, whose label reads Galang Gabaan has incorporated Kotpad in her designs. Sabyasachi Sathpathy, an Indian fashion designer who rose to fame with Big Boss 11, has incorporated kotpad fabric in his collection. I hope to see many more trendsetting fashion icons come forward to showcase the uniqueness of Kotpad. So let this be our collective responsibility to preserve the dying art for the next generation.
P.S.- My passion for handloom fabrics attracted one of my dear friend’s attention who is an Anthropology professor and deeply involved in a project to uplift and support indigenous artisans. Her project currently concentrates on weavers from Odisha and will eventually spread to other states. I joined her project as an advisory member for building a bridge to connect weavers to the global market. This project gained me access to delve into the weaver's world. It is unfortunate that most of these weavers compete against time. The world has moved on with modernization and mass production of synthetic fabrics while time stands still for these indigenous weavers.
It might be worth watching the following interview of Sadhguru here regarding toxic clothing.
Very informative and Brilliantly written.
A beautiful and passionate piece of writing
Well written. Enjoyed reading it